Fire-Rated Pipe Insulation Explained
The external corrosion of pipes poses a significant threat to the integrity and safety of pipelines, especially those in the oil and gas industry.
But understanding the causes and types of corrosion, as well as implementing effective prevention and mitigation strategies, can help us learn to maintain pipeline longevity and prevent costly mistakes.
Are you ready to learn about the types of corrosion and strategies to present them?
If so, keep reading!
Understanding the Causes of External Pipeline Corrosion
There are two main causes of pipeline corrosion, such as:
Environmental Contributors to Corrosion
External corrosion in pipelines is primarily driven by environmental factors:
- Soil composition
- Moisture levels, and
- Oxygen exposure play critical roles in accelerating corrosion
Soils with high conductivity, such as those containing salts or acidic compounds, can significantly increase the rate of corrosion.
Additionally, moisture and oxygen facilitate electrochemical reactions on the metal surface that can lead to material degradation over time.
Chemical Agents That Cause Corrosion
Contaminants such as chlorides, sulfates, and carbon dioxide contribute to the corrosion process. These chemicals, often present in the environment surrounding pipelines, react with the metal, and form corrosive compounds that weaken the pipeline structure. Stray currents from nearby electrical sources and microbial activity further exacerbate the corrosion, which leads to localized damage and pitting.
Types of External Corrosion
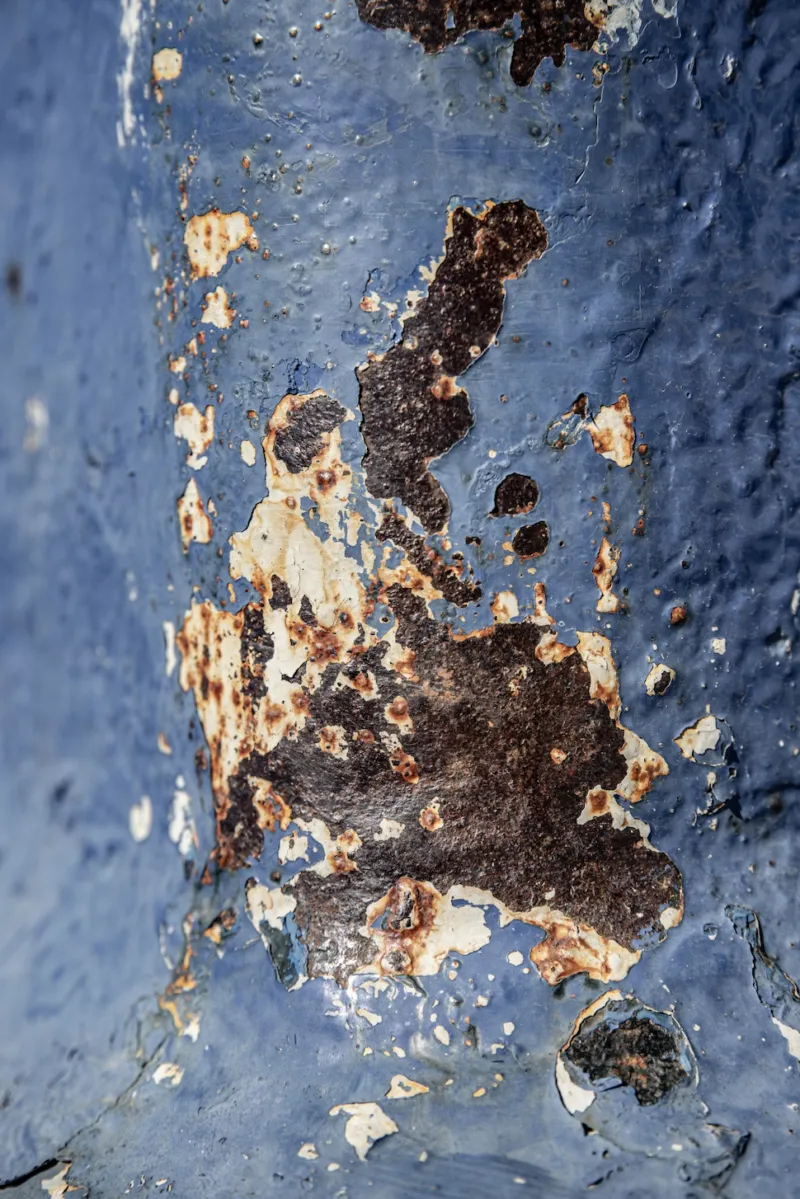
Although there are only two main types of causes to pipeline corrosion, there are several different types of corrosion. To name a few:
Uniform Corrosion
Uniform corrosion is characterized by an even thinning of the pipeline material across its surface. This type of corrosion occurs due to the consistent exposure of the pipeline to corrosive environments, which leads to a gradual loss of material over time.
For example, pipelines in rural areas with consistent exposure to atmospheric conditions may experience uniform corrosion. Although it may not cause immediate failure, uniform corrosion reduces the overall strength and durability of the pipeline.
Pitting Corrosion
Pitting corrosion is a localized form of corrosion that results in small, deep pits on the metal surface.
- Pits can penetrate the pipeline wall and points of weakness that are prone to leaks and ruptures.
- Pitting corrosion is particularly dangerous because it can occur rapidly and is often difficult to detect until significant damage has occurred.
For instance, pipelines transporting saline water are susceptible to pitting due to the aggressive nature of chloride ions.
Crevice Corrosion
Crevice corrosion occurs in confined spaces where the protective layer on the metal surface is compromised.
- Crevice corrosion is common in areas where pipelines are in contact with supports, gaskets, or other materials that create crevices.
- The lack of oxygen in these spaces disrupts the formation of a protective oxide layer, which leads to accelerated corrosion.
Examples include flanges and joints where water can become trapped and create a microenvironment that is conducive to corrosion.
Stress Corrosion Cracking (SCC)
Stress corrosion cracking is the result of the combined effect of tensile stress and a corrosive environment.
- SCC leads to the formation of cracks in the pipeline material, which can propagate and cause catastrophic failures.
- Pipelines subjected to high pressures or dynamic loads are particularly susceptible to SCC.
For example, pipelines in seismic zones or those experiencing frequent pressure fluctuations are at higher risk of SCC.
Microbiologically Influenced Corrosion (MIC)
Microbiologically influenced corrosion is caused by the presence and activities of microorganisms.
- These microorganisms produce corrosive byproducts such as hydrogen sulfide and organic acids, which attack the metal surface.
- MIC can lead to rapid and severe corrosion, often resulting in unexpected pipeline failures.
For instance, pipelines buried in wetlands or areas with high organic content in the soil are vulnerable to MIC due to the abundance of bacteria like SRB.
Effective Strategies to Prevent External Pipeline Corrosion
Protective Coatings
Applying protective coatings to pipelines is an effective strategy to prevent external corrosion.
- Coatings act as a barrier that shields the metal from corrosive environments.
- Common types of coatings include epoxy, polyurethane, and polyethylene.
- Epoxy coatings are widely used for their durability and strong adhesion properties.
- Regular inspection and maintenance of the coating are essential to ensure its integrity over time.
For instance, detecting and repairing minor damages in the coating can prevent major corrosion issues.
Cathodic Protection
Cathodic protection is an electrochemical method used to prevent corrosion by making the pipeline the cathode of an electrochemical cell.
- Cathodic protection is achieved by attaching sacrificial anodes or using impressed current systems.
- Cathodic protection effectively reduces the corrosion rate and extends the lifespan of pipelines.
Regular monitoring and maintenance are necessary to ensure the effectiveness of cathodic protection systems. For example, current cathodic protection systems require periodic adjustment and monitoring to maintain optimal protection levels.
Regular Maintenance and Monitoring
Implementing a robust maintenance and monitoring program is crucial for early detection and mitigation of external corrosion.
- Regular inspections, including visual assessments and advanced techniques like close interval surveys (CIS) and pipeline current mapping (PCM), help identify areas of concern.
- Maintenance activities such as cleaning, coating repair, and anode replacement should be carried out promptly to address any issues.
For instance, using non-destructive testing (NDT) methods can detect corrosion without damaging the pipeline.
External Corrosion Direct Assessment (ECDA)
External Corrosion Direct Assessment is a structured process that improves safety by assessing and reducing the impact of external corrosion on pipeline integrity.
- ECDA involves four phases: pre-assessment, indirect inspection, direct examination, and post-assessment.
- Continuous improvement process helps pipeline operators proactively address corrosion issues and maintain pipeline integrity
For example, indirect inspection methods like close interval surveys can identify potential corrosion hotspots, which are then examined directly to assess and mitigate corrosion damage.
Buckaroos® Products for Corrosion Prevention
Buckaroos ® offers a variety of products to prevent the external corrosion of pipelines—each taking their own unique roles.
Here are a few of our most popular products:
Pipe Insulation Saddles
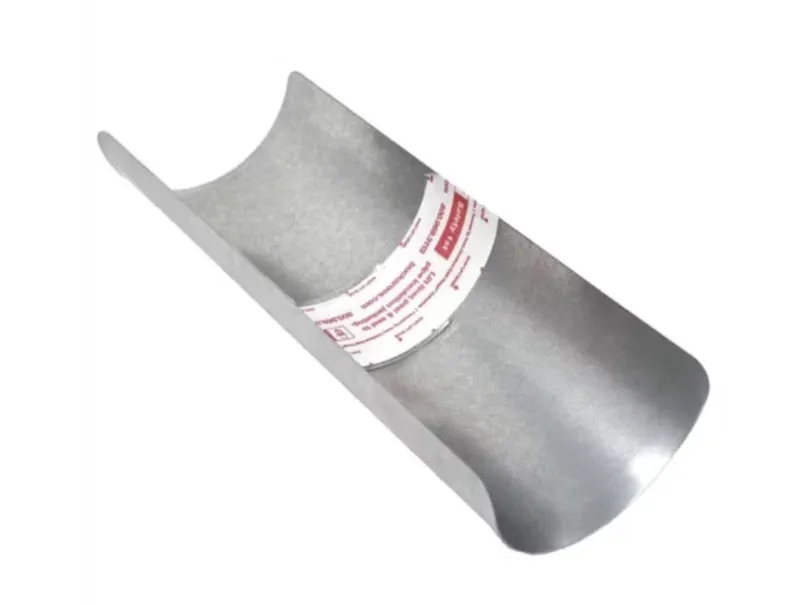
Our Pipe Insulation Saddles provide additional protection and insulation to pipelines to reduce the risk of corrosion, and they prevent direct contact between the pipeline and corrosive environments to help ensure that the pipeline remains protected.
Pipe Supports (Blocks and Dowels)
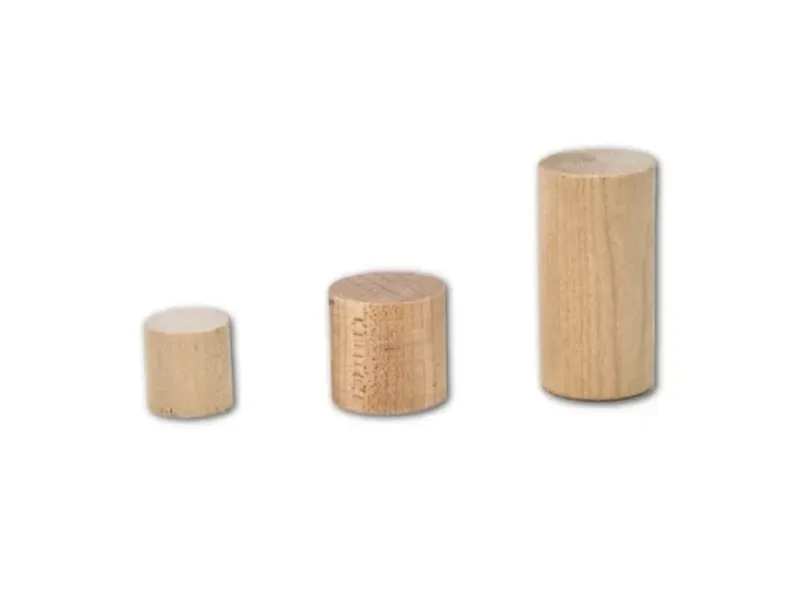
We also offer a range of products that offer additional support to pipelines, including blocks and dowels, that play a critical role in preventing direct contact with corrosive environments. These blocks and dowels.distribute loads evenly and minimize points of stress to help reduce the likelihood of corrosion.
Tru-Balance Insulated Supports
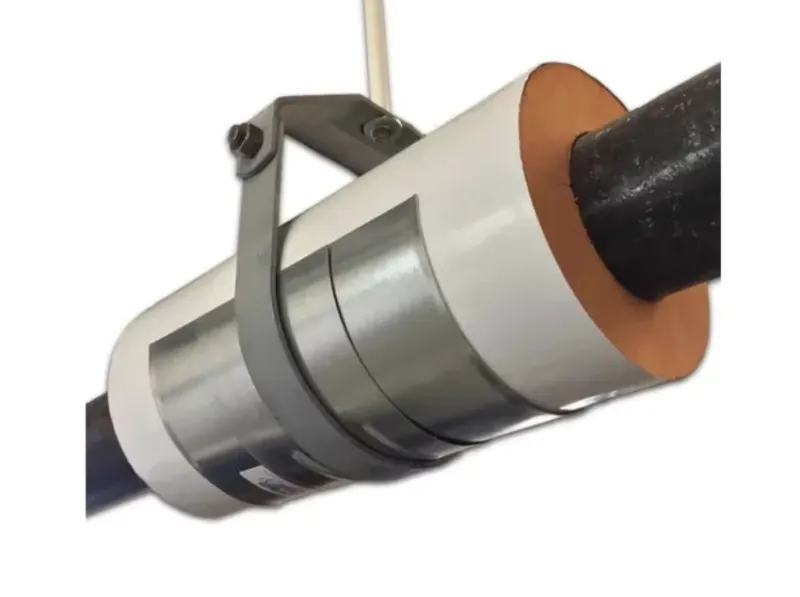
Another product of ours that offers support is The Tru-Balance™ Insulated Pipe Supports that ensure proper alignment and insulation of pipelines to further reduce the risk of corrosion. They are designed to provide thermal resistance and prevent moisture ingress, which can lead to corrosion.
Polyisocyanurate Insulation
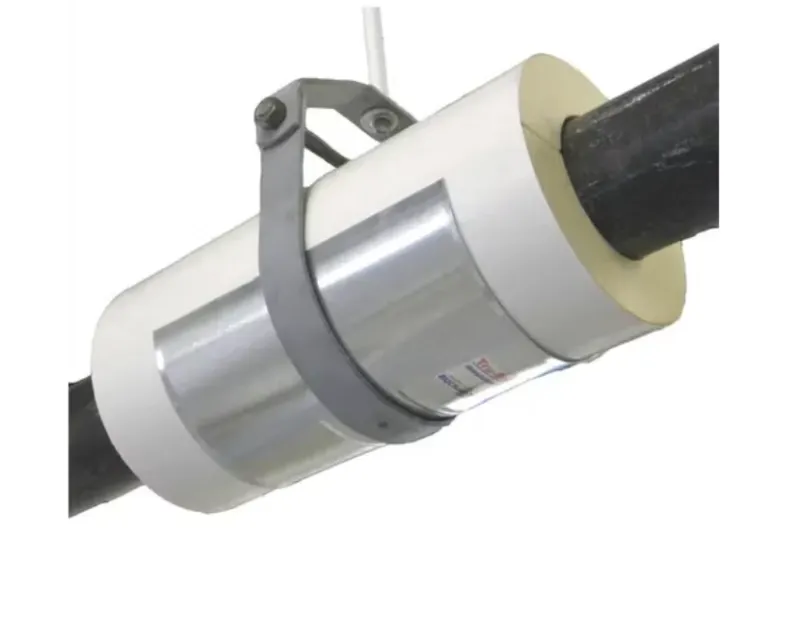
Buckaroos® polyisocyanurate insulation is an effective material for providing thermal resistance and preventing moisture ingress. It helps to maintain the integrity of the pipeline coating and reduces the risk of corrosion.
Shield Your Pipelines from Corrosion with Buckaroos®
Buckaroos® has a comprehensive range of solutions designed to combat external corrosion of pipelines.
By integrating advanced protective measures and utilizing our high-quality products, you can ensure the longevity and safety of your pipeline infrastructure.
Contact us today for more information!
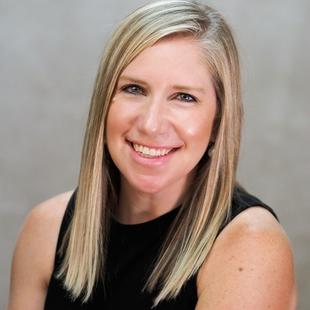
Carrie Powers
Carrie channels her passion for innovative solutions in the construction industry for Buckaroos. With a deep understanding of Buckaroos' leading insulated pipe support systems and insulation protection shields, Carrie ensures that building owners, engineers, and installers are well-equipped with the best tools and products. Her dedication to digital transformation and customer engagement helps Buckaroos maintain its reputation as a trusted resource for professional insulators across North America and Canada.
Featured articles
Industrial Pipe Hangers and Supports
Steam Pipe Insulation 101: Materials and Supports
8 Types of Pipe Supports and Their Features
Understanding Industrial Pipe Insulation and the Options