Fire-Rated Pipe Insulation Explained
Protecting pipelines from corrosion, preventing it, and controlling pipeline deterioration are essential for the pipeline industry.
To understand this more, let’s take a closer look at the innovative pipeline corrosion protection methods and products that are being used to protect pipelines against corrosion harmful—and in some cases, deadly—effects.
Traditional and Innovative Pipeline Corrosion Protection Methods
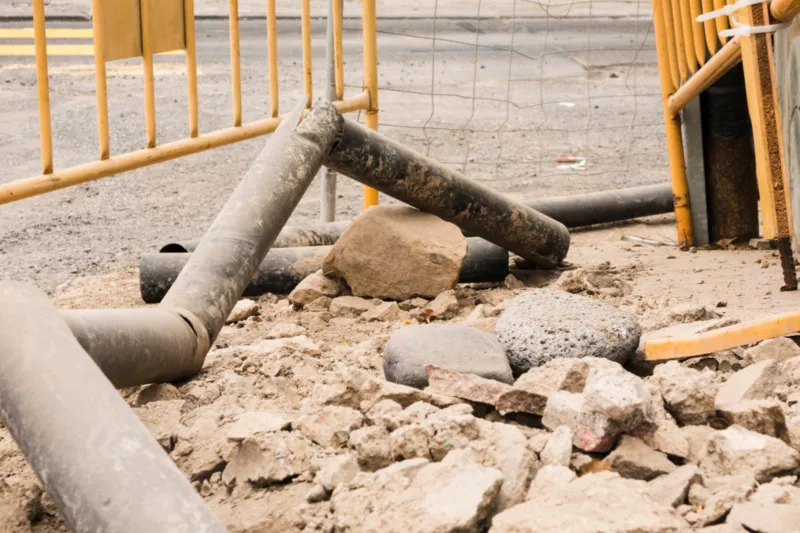
When exploring pipeline corrosion protection methods, it’s important to differentiate between the traditional methods, which have proven to be effective over time, and new solutions, which have become more prevalent in handling today’s challenges.
Traditional Methods
1. Cathodic Protection
A cornerstone of pipeline corrosion prevention, cathodic protection uses electrical currents to mitigate the electrochemical reactions that lead to corrosion. This method is especially effective in environments susceptible to electrolytic action.
2. Protective Coatings and Linings
Protective coatings and linings act as physical barriers that isolate the pipeline material from corrosive elements. Advances in materials science have led to the development of coatings like polyolefin systems, epoxy, and Polyguard’s RD-6® Coating System that provide robust protection against diverse forms of corrosion.
3. Corrosion Inhibitors
The strategic use of corrosion inhibitors introduces chemicals that form a protective film on the pipeline’s internal surfaces to significantly slow corrosion rates. Products like Polyguard IRO™ and IRO HD™ exemplify the effectiveness of these inhibitors by offering additional abrasion resistance and enhancing pipeline integrity.
4. Material Selection and Design Considerations
Selecting appropriate materials and incorporating corrosion resistance into the pipeline design phase are proactive measures that significantly reduce the likelihood of corrosion. Alloys containing chromium or molybdenum, for instance, offer improved corrosion resistance, which underpins the importance of material science in corrosion prevention.
Innovations in Pipeline Corrosion Protection
5. Pre-Construction Strategies for Corrosion Prevention
A vital aspect of pipeline construction that aids in corrosion prevention involves environmental consideration and pre-treatment of materials.
- Techniques like trenchless technology are employed to minimize soil disruption, and reduce the potential for electrochemical corrosion.
- Additionally, positioning pipelines away from pollution sources or industrial areas lessens their exposure to corrosive substances.
- Applying protective primers to pipes before assembly offers an early defense layer against corrosion.
Integrating these strategies during the construction phase establishes a robust foundation for a corrosion-resistant pipeline network.
6. Flange and Joint Isolation
Implementing flange and joint isolation is key to preventing electrochemical reactions between dissimilar metals. This method effectively interrupts the metallic path which is crucial for controlling the flow of electrical currents in cathodic protection systems, and is vital for the integrity of pipelines where materials intersect.
7. Use of Fiber-Reinforced Polymers
Fiber-reinforced polymers (FRPs) represent a cutting-edge solution for repairing and strengthening pipelines. Offering substantial resistance to corrosion and mechanical stresses, FRPs are an innovative means to prolong the operational life and enhance the reliability of pipeline systems against the persistent challenge of corrosion.
8. Regular Maintenance and Monitoring
While maintenance is a traditional practice, the use of the latest inspection technologies to detect and mitigate corrosion issues represents an evolution towards more innovative approaches. Implementing regular maintenance schedules and utilizing the latest in inspection technology are essential for early detection and mitigation of potential corrosion issues to help ensure the pipeline’s integrity and operational safety.
Method | Type | Applicability | Limitations |
---|---|---|---|
Cathodic Protection | Traditional | Widely applicable, especially effective in environments prone to electrolytic action | Requires power source, regular monitoring for effectiveness |
Protective Coatings and Linings | Traditional | Universal applicability, advances in materials science offer robust protection | Subject to degradation over time, requires periodic reapplication or inspection |
Corrosion Inhibitors | Traditional | Effective in internal corrosion control, enhanced by advanced chemical formulations | Effectiveness dependent on consistent internal conditions, may require regular replenishment |
Material Selection and Design | Traditional | Critical in initial design phase, choice of materials can vastly reduce corrosion likelihood | Increased upfront cost, requires detailed knowledge of environmental conditions |
Pre-Construction Strategies | Innovative | Minimizes environmental impact, early application of protective measures | Requires comprehensive planning and environmental assessment, potential upfront cost increase |
Flange and Joint Isolation | Innovative | Prevents electrochemical reactions between dissimilar metals, crucial in mixed-material designs | Design complexity may increase, requires meticulous installation |
Use of FRPs | Innovative | For repair and reinforcement, offers high resistance to mechanical stresses and corrosion | Initial cost and specialized installation, limited by the type of pipeline material |
Regular Maintenance and Monitoring | Innovative | Essential for integrity, evolved with technology for early detection and mitigation | Dependent on technological advancement, requires regular schedule and expert analysis |
This chart helps highlight the balance between traditional methods that rely on proven techniques and innovative approaches that leverage the latest technologies and materials to combat corrosion.
Understanding the Types of Corrosion and Their Impact
Understanding the complex issue of pipeline corrosion is crucial. It comes in different forms, each affecting pipeline integrity in its own way:
Galvanic Corrosion
This happens when different metals touch in a corrosive environment, causing one of them to corrode faster. Choosing materials that are similar in the galvanic series can greatly lower the risk of galvanic corrosion to make pipeline components last longer and more evenly.
Pitting Corrosion
Pitting corrosion is known for causing aggressive, localized damage that leads to small, deep pits. It’s especially tricky because it can remain hidden until significant damage occurs. To catch and reduce pitting corrosion early, it’s crucial to have regular, thorough inspections and apply specific protective coatings.
Stress Corrosion Cracking (SCC)
SCC happens when tensile stress and a corrosive environment work together on a material that can’t handle it, causing cracks to form and grow. To prevent SCC, it’s important to design with minimal stress points and choose materials less likely to crack under the environmental conditions they’ll face.
Advanced Technologies and Materials
The advent of advanced materials and technologies, including thermally sprayed aluminum (TSA) and fluoropolymer coatings, offers superior protection against both external and internal corrosion challenges. These materials not only extend the life of pipelines, but also enhance their reliability in harsh operational environments.
The Role of Buckaroos® in Pipeline Corrosion Protection
Buckaroos® offers targeted solutions to combat pipeline corrosion, each designed with cutting-edge technology to bolster the durability and safety of pipeline systems:
CleviShield™ Insulated Pipe Supports
CleviShield™ Insulated Pipe Supports prevent direct metal-to-pipe contact to reduce thermal bridges and moisture accumulation, which are common causes of corrosion.
CoolDry™ Insulated Pipe Supports
CoolDry™ Insulated Pipe Supports offer enhanced moisture control to protect pipelines from the corrosive effects of condensation.
Roundup Plus™ Saddles
Designed for stability and durability, Roundup Plus™ Saddles provide secure pipe positioning to mitigate risks of damage and subsequent corrosion.
Each product exemplifies Buckaroos® commitment to innovation in pipeline safety and efficiency.
Engage with Buckaroos® for Enhanced Corrosion Protection Solutions
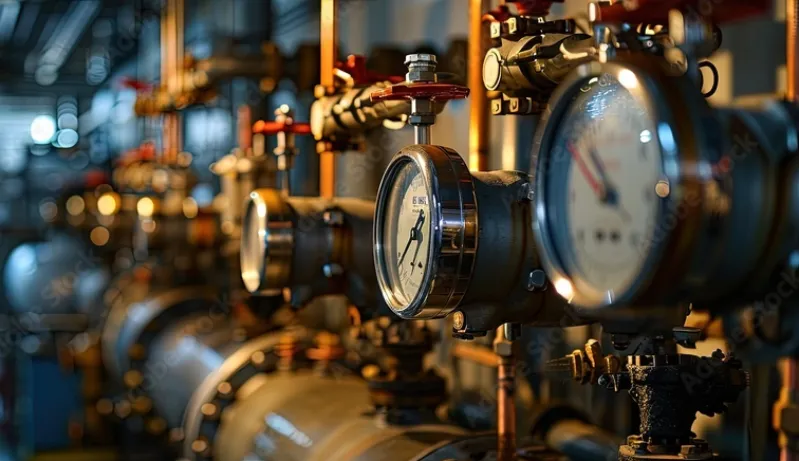
At Buckaroos®, we know how important pipeline integrity is for your operations. We’ve developed a range of products focused on providing top-notch pipeline corrosion protection to keep your pipeline system strong and dependable.
Get in touch today to talk with one of our experts
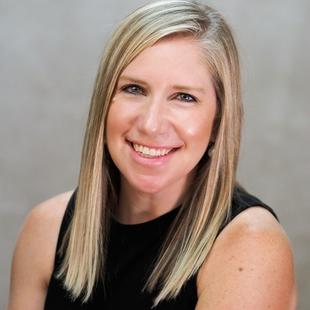
Carrie Powers
Carrie channels her passion for innovative solutions in the construction industry for Buckaroos. With a deep understanding of Buckaroos' leading insulated pipe support systems and insulation protection shields, Carrie ensures that building owners, engineers, and installers are well-equipped with the best tools and products. Her dedication to digital transformation and customer engagement helps Buckaroos maintain its reputation as a trusted resource for professional insulators across North America and Canada.
Featured articles
Industrial Pipe Hangers and Supports
Steam Pipe Insulation 101: Materials and Supports
8 Types of Pipe Supports and Their Features
Understanding Industrial Pipe Insulation and the Options