Fire-Rated Pipe Insulation Explained
Chilled Water Pipe Insulation: Types, Processes, and Questions
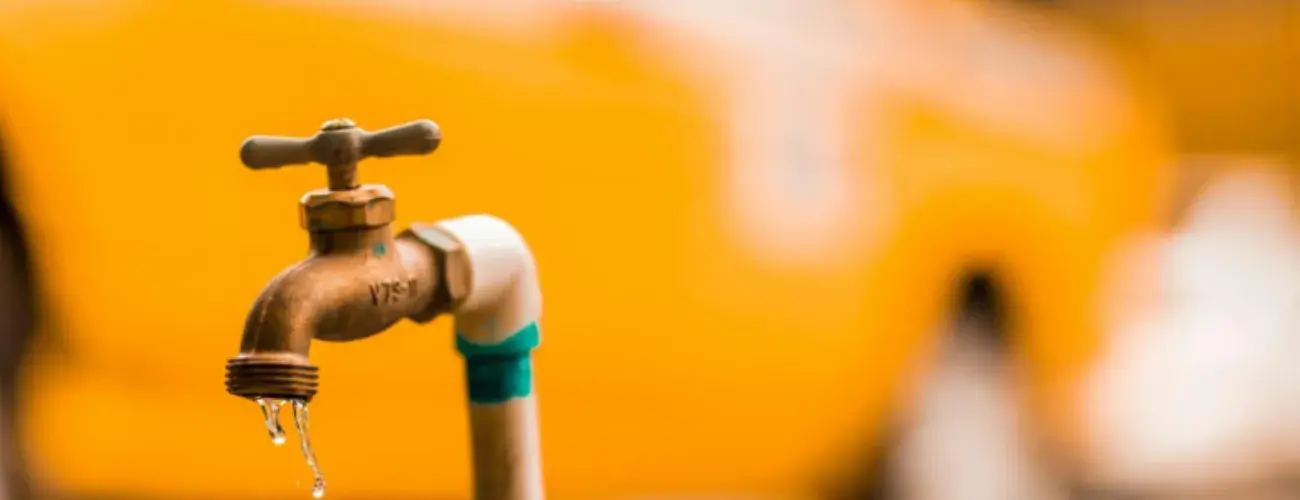
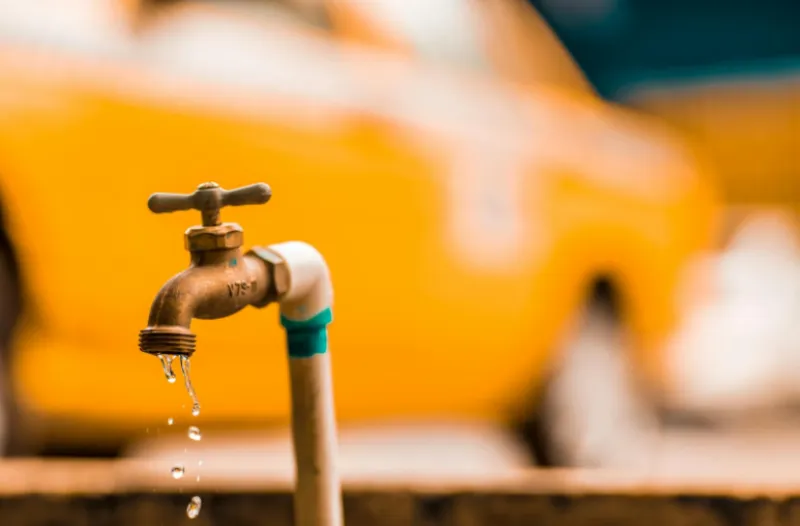
Chilled water pipe insulation plays a crucial role in the efficient operation of HVAC systems in buildings by maintaining the water’s low temperature. This guide explains the importance of chilled water pipe insulation, its purpose, the different materials used, application methods, and best practices.
Understanding Chilled Water Pipe Insulation
Chilled water pipe insulation is the protective layer that workers install on the water pipes running through a building’s HVAC system. Whether in an office building’s cooling system or an industrial freezer unit, the insulation maintains the water’s low temperature for efficient chiller performance and energy conservation.
The Importance of Chilled Water in HVAC
HVAC systems rely on chilled water to regulate environmental conditions. By harnessing the principles of thermodynamics, these systems extract heat from indoor air and transfer it to the chilled water returning from the building, which then cycles through the chiller to be cooled once more. Effective insulation ensures minimal energy loss across the distribution pipes to optimize the operational economy and environmental footprint.
Types of Insulation for Chilled Pipes
There are several types of insulation used for chilled water pipes, each with its unique properties and ideal applications. Fiberglass, elastomeric foam, polyisocyanurate, and phenolic foam are common, with a selection process largely driven by factors such as temperature requirements, moisture sensitivity, and spatial constraints.
The Purpose of Chilled Pipe Insulation
The purpose of chilled pipe insulation extends beyond creating a thermal barrier. It also prevents condensation, corrosion, reduces impact, and offers acoustic dampening, all while meeting health and safety regulations.
Choosing the Best Insulation for Chilled Water Pipes
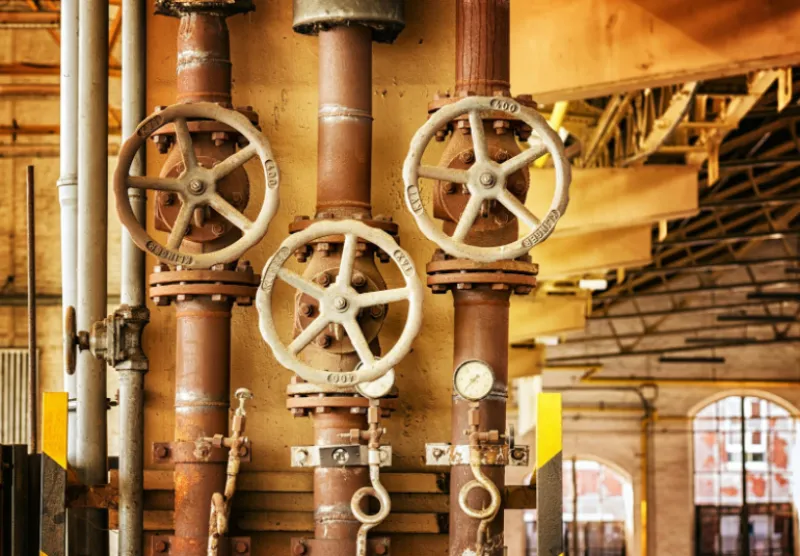
With a plethora of options in the market, selecting the right insulation for chilled water pipes is a critical decision. Here we dissect the factors that should influence your choice, from material properties to long-term performance considerations:
Material Specification and Properties
Navigating the technical specifications and performance metrics of insulation materials can be daunting. However, understanding key indicators such as thermal conductivity, compressive strength, and flammability ratings is paramount to making an informed choice.
How to Insulate Chilled Pipes
The method of insulation also plays a significant role. Factors such as the installation environment, pipe configuration, and system shutdown constraints influence whether you should opt for pre-slit tubes, spray foams, or rigid boards.
Indoor vs. Outdoor Insulation
The variability that indoor and outdoor environments introduce requires tailored insulation strategies. While outdoor applications demand UV resistance and weather protection, interior settings emphasize anti-microbial properties and fire safety compliance.
Insulating Your Chilled Water Pipes: The Process Explained
The installation process of chilled water pipe insulation directly impacts its efficiency and longevity. We break down the key steps from preparation to final review for a seamless installation:
1. Gather the Necessary Tools and Materials
The importance of preparation cannot be overstated. Distinct tools like tie tape, stainless steel bands, and specialized adhesives are essentials that must be ready for use.
2. Secure the Work Area and Prepare the Pipes
Safety measures should guide the preparation stage, from shutting off the water supply to cleaning and priming the pipe surfaces to ensure a secure bond with the insulation.
3. Apply the Insulation
The application phase is a delicate balance of precision and speed. Whether it’s using an adhesive for flexible elastomeric foam or stitching mastics for fiberglass, the chosen method must guarantee an airtight seal and full coverage.
4. Finishing and Quality Control
Properly seal all seams and joints to protect against external elements, and conduct thorough quality checks to conclude the insulation process in order to set the stage for reliable long-term performance.
FAQs: Chilled Water Pipe Insulation Demystified
To address the common inquiries surrounding chilled water pipe insulation, we’ve compiled a list of frequently asked questions. This section tackles queries about insulation thickness, maintenance, re-insulation, and compliance with industry standards.
How Thick Should Chilled Pipe Insulation Be?
Determining the optimal insulation thickness involves a consideration of environmental conditions, cost, and the requisite control over heat gain or loss. Industry standards often provide tables correlating pipe diameter with recommended insulation depths for nominal thermal efficiency.
What Is the Maintenance Cycle for Chilled Pipe Insulation?
Regular visual inspections can often reveal signs of wear or damage that may compromise the insulation’s function. A preventative maintenance schedule should include checks for water ingress, physical deterioration, and the integrity of seals and support structures.
When Is Re-insulation Necessary and How Is It Done?
Exposure to environmental factors, changes in system requirements, or wear over time can warrant re-insulation. The process typically involves removing the old insulation, preparing the pipe surface, and meticulously installing new insulation to restore and enhance the system’s performance.
Are There Industry-Specific Regulations for Chilled Water Pipe Insulation?
Various organizations and regulatory bodies issue guidelines that set the benchmark for insulation standards by addressing aspects such as thermal efficiency ratings, R-values, and the materials allowed for use in specific contexts. Adherence to these regulations is integral to securing operational permits and ensuring the safety and sustainability of the installation.
The Role of Insulation Pipe Supports and Saddles in Chilled Water Systems
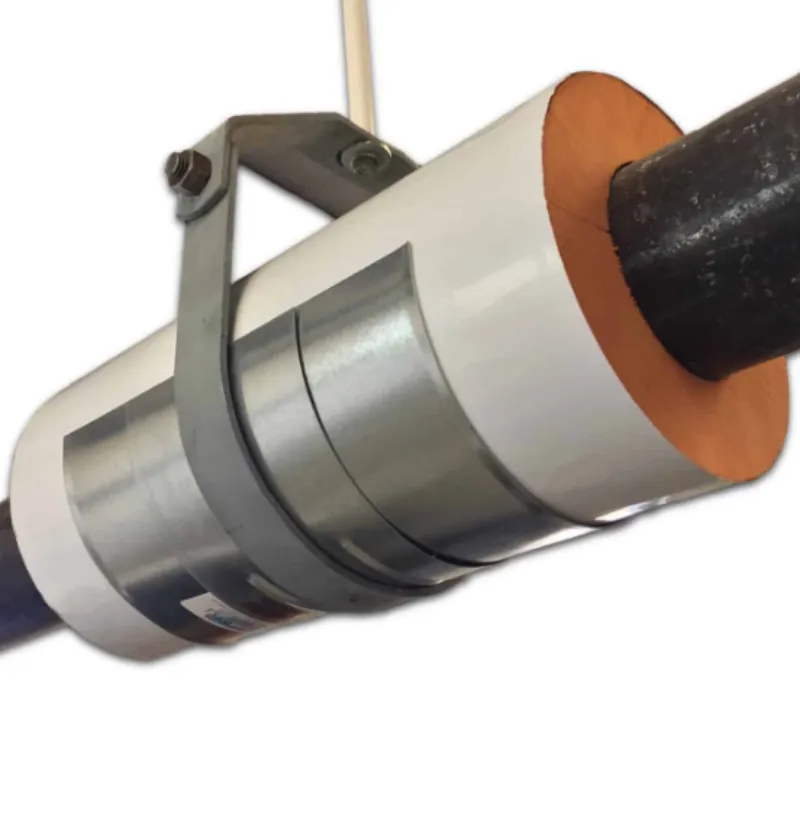
Buckaroos® introduces innovative solutions for chilled water systems with CoolDry™ Insulated Pipe Supports and Pipe Saddles. These solutions are not just about preventing heat gain or loss; they also focus on durability and ease of installation, which makes them suitable for a wide range of commercial and industrial applications.
Their design addresses common challenges such as condensation and thermal bridging to ensure that systems remain energy efficient and structurally sound over time.
Elevate Your Chilled Water Pipe Insulation with Buckaroos® Support Solutions
Don’t wait to enhance the efficiency and longevity of your chilled water piping system.
Explore Buckaroos® range of pipe saddles and insulated pipe supports, and take the first step towards minimizing energy loss and extending the life of your insulation. Our expert team is ready to guide you through selecting the perfect products tailored to your needs.
Contact us today for more information!
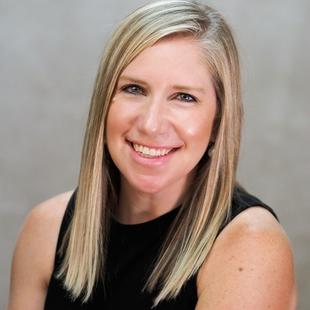
Carrie Powers
Carrie channels her passion for innovative solutions in the construction industry for Buckaroos. With a deep understanding of Buckaroos' leading insulated pipe support systems and insulation protection shields, Carrie ensures that building owners, engineers, and installers are well-equipped with the best tools and products. Her dedication to digital transformation and customer engagement helps Buckaroos maintain its reputation as a trusted resource for professional insulators across North America and Canada.
Featured articles
Industrial Pipe Hangers and Supports
Steam Pipe Insulation 101: Materials and Supports
8 Types of Pipe Supports and Their Features
Understanding Industrial Pipe Insulation and the Options